COPPER CHROMIUM ZIRCONIUM
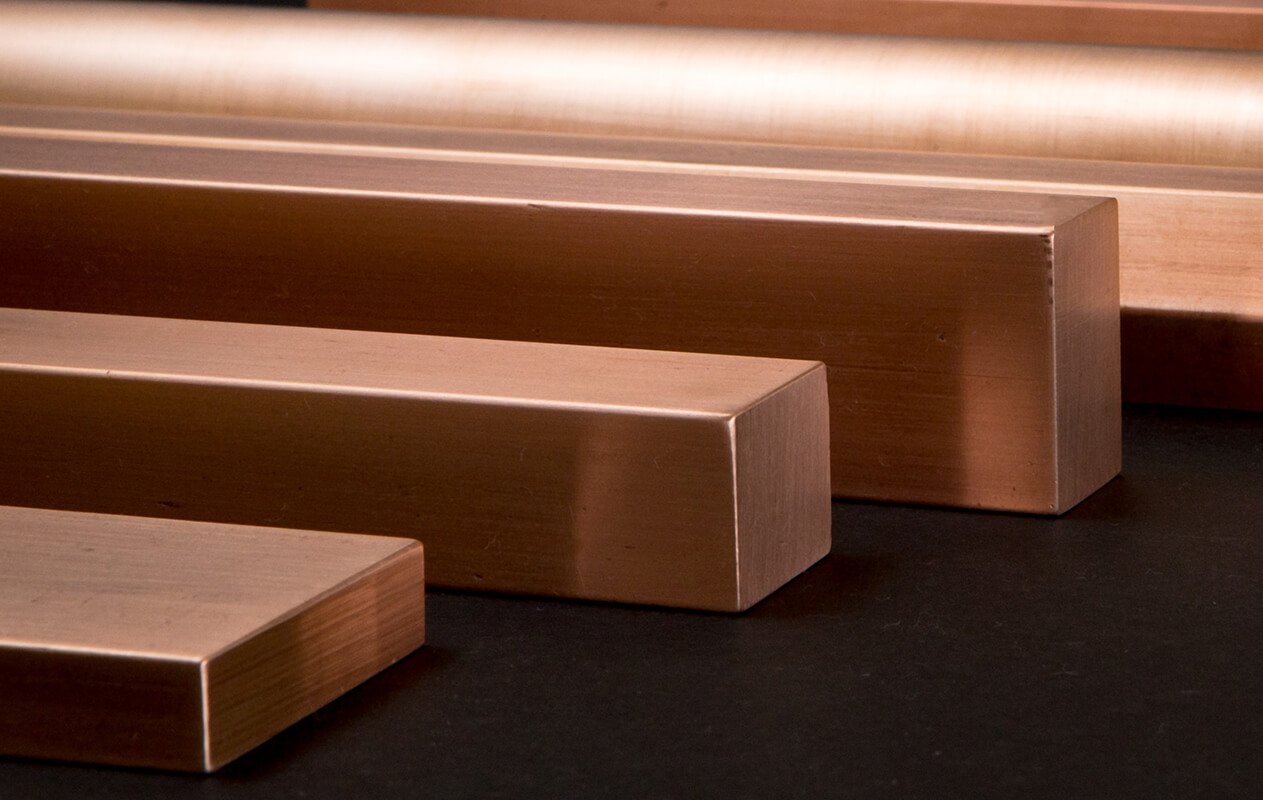


Copper Chromium Zirconium C18150, RWMA Class 2, AWS J1.3
Copper Chromium Zirconium Alloy has the addition of zirconium to chromium copper to improve creep resistance at high operating temperatures and reduces sticking of electrodes to the work during spot welding of galvanized/coated materials. C18150 is specified mainly for electrode applications. Copper Chromium Zirconium is an RWMA Class 2 material and is stronger than the RWMA Class 1 materials.
Chemical Compositions of RWMA Materials Group A - Copper Base Alloys |
|||||
RWMA Class |
UNS Number |
Description |
Cu |
Cr |
Zr |
2 |
C18150 |
Chromium Zirconium Copper |
Balance |
0.5 – 1.5% |
0.02 – 0.20% |
Cu: Copper
Cr: Chromium
Zr: Zirconium
Available in Rod, Bar, Plate, Wire/Coil.
Typical usages of RWMA Class 2 Copper Alloy: C18150 is recommended for spot and seam, welding cold and hot rolled steels, coated materials, current-carrying shafts and arms, back-up bars for both resistance and arc welding, and electrical current carrying structural parts.
It is used extensively for cap-style resistance welding electrodes. It can provide less sticking and resistance for much longer than its counterpart copper -chromium in some specific situations.
GENERAL USES OF C18150 |
|||
Back-up Electrodes |
Bushings |
Caps & Shanks |
Casting Wheels |
Centrifugal Casting Molds |
Circuit Breaker Parts |
Collector Connector |
Collector Housing |
Connector Bar |
Connectors |
Connection Lead Bar |
Continuous Casting Molds |
Cross Wire Welding Electrodes & Components |
Damper Ring/Finger |
Dies & Fixtures |
Electrode Holders and Adaptors |
Electrical & Mechanical Power Components |
Flash & Butt Welding Dies |
Flexible Connector |
Heat Flux Components |
Injection Blow Molds & Dies |
Lead Conductor Bar |
Motor End Rings |
Neutral Bus Bar |
Non-Sparking Applications |
Nut & Stud Welding Electrodes |
Power Generation Products |
Power Semiconductor Bases |
Resistance Welding Electrodes |
Rotor Coil Bars |
Seam Weld Wheels |
Series Loop Segment |
Shafts |
Slip Rings |
Slot Wedge |
Snap Rings |
Special Nipple |
Sputtering Target Backing Plates |
Terminal Box Connectors |
Threaded Electrodes |
Transmission Devices |
Water Clip |
Welding Arms |
Welding Connectors |
Welding Platens |
Wire for Additive Manufacturing |
Item Name: | Copper Chromium Zirconium Alloy C18150 |
RWMA (Resistance Welding Manufacturing Alliance) Class: | Class 2 |
Principal Element: | Cu, Cr, Zr |
Minimum Hardness Rockwell (up to 1" dia.): | HRB 75 |
Minimum Electrical Conductivity (% IACS): | 75 |
Metal Stock Availability: | Stocked in mill form or precision cut to your specifications. |
Shape: |
Wire/Coil Bar |
Length for Round, Hexagon, Square, Octagon, Rectangle, Special Shapes: | All sizes in standard lengths up to 12 ft Special Sizes |
Diameter for Round, Hexagon, Square, Octagon, Rectangle, Special Shapes: | 1/8 to 15 1/8 in Special Sizes |
Thickness for Plate: | 1/8 to 10 in Special Sizes |
Click here for information on Rolled and Forged Plate
Quality Assurance
Quality Policy: Cadi Company Inc. is dedicated to world-class excellence. Our commitment is to continually achieve the highest standards required to meet our customer’s needs. Cadi is committed to a policy of continuous improvement within all areas of the organization through customer communication, by means of quality planning and review, as well as employee training and participation to achieve the Cadi commitment goal of 100% in quality, effectiveness, and customer satisfaction.
Quality Objectives: Cadi Company, Inc. is committed to the development and implementation of the ISO Quality Management System. We pledge that through the efforts of all our employees working together as a team, we will continually strive to be a leader (in our markets) in satisfying our customers’ needs with regard to service, performance, and competitive pricing. Cadi shall maintain global and domestic sources to provide quality products as required by our customers. Cadi will provide our customers with the highest level of satisfaction by achieving the goal of 100% in the areas of product quality and on-time delivery performance.
Cadi Company is committed to providing goods and services that meet or exceed our customer’s requirements and expectations. It is our firm belief that this dedication to the highest standards is the cornerstone of our existence.
- We have the equipment and processes to guarantee the quality of the products we manufacture.
- We continually upgrade our equipment and have ongoing training company-wide.
- Each order undergoes stringent Quality Assurance Processes to assure accuracy and precision to the client’s specifications and is verified throughout the manufacturing cycle with scheduled quality assurance audits.
- All material is subject to detailed physical tests where microstructures, tensile, yield strength, U.T. testing, eddy current conductivity, elongation, and hardness are measured and reported.
- Climate-controlled inspection facility.
- We have a Metallurgical Engineer on-site for any technical questions.
To ensure Cadi follows rigorous quality and procedural protocols we are ISO 9001:2015 Certified and have been for over 18 years.
ISO Certification: | 9001:2015 (Registration # 10002745 QM15 Valid until 2027-08-21) |
Reports: | Certification of Compliance Chemical Analysis Final Inspection Material Test Reports |
Mechanical and Physical Testing: | Elongation Grain Size Hardness Tensile Yield |
Nondestructive Testing: | Chemical Analysis Conductivity Liquid Penetrant Ultrasonic X-Ray |
Alloy Applications Cross Reference Chart | C15000 | C18150 | C18000 | C18200 | C17510 | C17200 | C15760 |
Axial Conductors | X | - | - | - | - | - | - |
Back-up Electrodes | X | X | X | X | X | X | X |
Bushings | X | X | X | X | X | - | - |
Caps & Shank | X | X | X | X | X | X | X |
Casting Wheels | X | X | - | X | - | - | - |
Casting Wheels and Dam Blocks | - | - | X | - | X | X | - |
Centrifugal Casting Mold | X | X | X | X | - | - | - |
Circuit Breaker Parts | X | X | - | X | - | - | X |
Collector Connector | X | X | - | X | - | - | - |
Collector Housing | X | X | - | X | - | - | - |
Connector Bar | X | X | - | X | - | - | - |
Connectors | X | X | X | X | X | - | X |
Connection Lead Bar | X | X | - | X | - | - | - |
Continuous Casting Molds | X | X | X | X | X | X | - |
Cross Wire Welding Electrodes & Components | X | X | X | X | X | X | X |
Damper Ring/Finger | X | X | X | X | - | - | - |
Dies & Fixtures | X | X | X | X | X | X | - |
Die Casting Pistons | - | - | X | - | X | X | - |
Die Casting Plunger Tips | - | - | X | - | X | X | - |
Electrode Holders & Adaptors | X | X | X | X | X | X | - |
Electrical & Mechanical Power Components | X | X | X | X | X | X | X |
Flash & Butt Welding Dies | X | X | X | X | X | X | X |
Flexible Connector | X | X | - | X | - | - | - |
Heat Flux Components | X | X | X | X | X | - | X |
Injection Blow Molds & Dies | - | X | X | X | X | X | - |
Joining Components | X | - | X | - | X | X | X |
Lead Conductor Bar | X | X | - | X | - | - | - |
Motor End Rings | X | X | X | X | X | - | - |
Neutral Bus Bar | X | X | - | X | - | - | - |
Non-Sparking Applications | - | X | X | X | X | X | - |
Nut & Stud Welding Electrodes | X | X | X | X | X | X | - |
Performance Engine Components | - | - | X | - | X | X | - |
Permanent Molds | - | - | X | - | X | X | X |
Power Generation Products | X | X | X | X | - | - | - |
Power Semiconductor Bases | X | X | - | X | - | - | - |
Resistance Welding Electrodes | X | X | X | X | X | X | - |
Rotor Coil Bar | X | X | - | X | - | - | - |
Seam Weld Wheels | X | X | X | X | X | X | - |
Series Loop Segment | X | X | - | X | - | - | - |
Shafts | X | X | X | X | X | X | - |
Slip Rings | X | X | - | X | - | - | - |
Slot Wedge | X | X | X | X | - | - | - |
Snap Rings | X | X | - | X | - | - | - |
Special Nipple | X | X | - | X | - | - | - |
Sputtering Target Backing Plate | X | X | X | ||||
Terminal Box Connectors | X | X | - | X | - | - | - |
Threaded Electrodes | X | X | X | X | X | X | - |
Transmission Devices | X | X | - | X | - | - | X |
Water Clip | X | X | - | X | - | - | - |
Wear Plates | - | - | - | - | - | X | - |
Welding Arms | X | X | X | X | X | X | - |
Welding Blocks | X | - | X | - | X | X | - |
Welding Connectors | X | X | X | X | X | X | - |
Welding Platens | X | X | X | X | X | X | - |
NOTE: C18150 Copper Chromium Zirconium and C15000 Copper Zirconium are both good replacements for C16200 Copper Cadmium. C18150 Copper Chromium Zirconium is a good replacement because of its precipitation hardened copper alloy that provides high strength at elevated temperatures with good conductivity. C15000 strength properties are developed through cold working (similar to C16200) whereas C18150 strength properties are developed primarily from heat treating (precipitation hardening), which is an advantage for large parts.
What is C18150 Copper? Known as copper chromium zirconium it offers excellent conductivity, weldability, and workability. Great for spot and seam welding and used extensively for cap-style resistance welding electrodes. It can provide less sticking and resist deformation for much longer that its copper-chrome counterparts in some specific situations.
What is Copper Chromium Zirconium? Copper Chromium Zirconium Copper Alloys are high copper alloys that contain 0.5 to 1.5% chromium and 0.02 – 0.20% zirconium, and the balance is high quality copper. The chromium copper alloys are used for their high strength, corrosion resistance and electrical conductivity.
Other References For C18150: CuCrZr Alloy, CuCrZr Copper Alloy, Chromium Zirconium Copper Suppliers, C18150 Mechanical Properties, Corson Bronze, Corson Alloy, CDA C18150, Ampcoloy 972 (equivalent), UNS C18150 and C18150 RWMA Class 2 Alloy, .